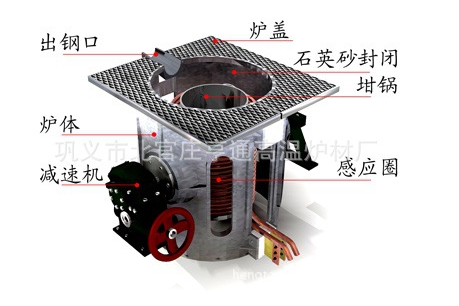
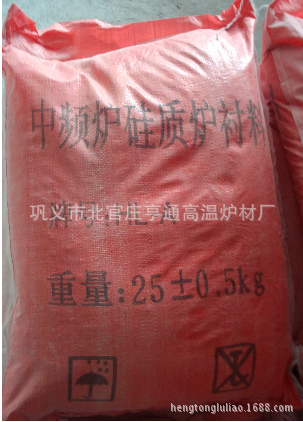
石英砂捣打料 采用预相变处理的硅矿为原料,明显的改善了炉衬的膨胀弊端,烘炉时炉衬上涨幅度明显降低,冷炉时无裂纹.它的特点是原料高纯,级配合理、抗急冷急热,耐高温,耐腐蚀尤其适合于大型中频电炉的间歇式作业。此材料系预混的干捣混合料,根据顾客需求已配好各种添加剂可直接使用。不同的炉子不同的配方。系成品混合料。采用25公斤的编织袋包装。
石英砂捣打料技术数据(化学成份不含烧结剂):
SiO2 ≥ 98.5% CaO+MgO ≤0.1% Fe2O3≤ 0.2%
材料密度:2.1g/cm3 最高使用温度:1750℃ 施工方法:干振或干捣
石英砂捣打料主要用于中频炉冶炼:灰生铁,铸钢,球墨铸铁,低合金钢,普碳钢,炼铜,炼铝等。
石英砂复合捣打料
石英砂捣打料是由硅砂和粘结剂、硼酸等构成,主要成份和矿物组成比较单一。经实践发现、单纯使用石英砂打炉料,无论如何改变配比,炉衬使用寿命仍不理想。而它的主要成分SiO 2 是一种多种晶型矿物原料 ,在高温下,它的主晶成份与低熔点物质结合,从而促使玻璃相过早出现。故荷重软化开始温度大大降低,并且α-石英时转变为α-鳞石英时体积膨胀达+16%,衬体的内部结构变的蔬松也是衬体损毁的重要原因。只有α-鳞石英的温度控制在1470℃以内,才能保持稳定不变;而工作温度已接近或等于炉衬荷重软化温度时,其体积由膨胀转为收缩-0.9%。α-鳞石英极不稳定,在转变α-方石英晶型和结晶玻璃时,炉衬内即产生很大的热内应力,最终出现裂纹和龟裂、剥落,铜水渗入衬内,短时间内炉底石就会烧穿、漏炉,造成炉衬报废。
总之,使用单一的硅砂做炉衬,它的急冷、急热、抗渣、抗蚀及隔热和抗机械冲击性能都有不同程度的降低,这是造成炉衬使用寿命短的根本原因。
根据上述情况分析,单纯的硅质材料炉衬不是很理想,不能满足冶炼产品。
我们为了满足广大用户的冶炼产品的生产需要,广大工程技术人员在硅质材料基础上经过多年的研究,现已研究开发出了新型复合硅质耐火材料,该材料的问世,解决了冶炼炉龄低,抗侵蚀,抗腐蚀的熔化问题,欢迎广大用户使用,现作以下简介:
石英砂复合捣打料的矿物组成:由石英、陶瓷复合粘结剂、熔融石英、抗渗剂等多种材料配制成。经大吨位和小吨位众多企业使用验证,它具有以下特点:
1)烧结层薄;
2)提高热效率;
3)在高温时物理化学变化小;
4)保温性能好;
5)衬内气孔致密度好,膨胀 系数小;
6)导电、导热性小;
7)表面结构强度好,不裂纹、不剥落;
8)体积稳定,抗冲刷、
9)抗侵蚀;
10)使用寿命长。
应用范围:
总之,新型复合硅质捣打料终于解决了长期以来冶炼加工企业梦寐以求的愿望。虽该材料比传统石英砂捣打料成本高出3-4倍,但无论从经营运作的观点来分析,还是从经济上讲都比较实惠。尤其是大吨位炉衬和特种合金炉衬寿命成倍提高,核算成本不但没有提高,相反成本还降低许多,而且还提高了产品质量,降低了金属烧损耗量,给企业节能降耗,提高效益提供有利条件。
石英砂打炉料使用说明:
干式打结炉衬(以2t中频无芯感应炉为例):
线圈绝缘胶泥的应用:2t中频无芯感应炉的感应圈涂覆有绝缘胶泥层。与感应路通常使用的绝缘材料云母、玻璃丝布等相比,使用线圈绝缘胶泥有如下好处
:第一,烘干后,厚度为8-15mm的线圈绝缘胶泥层具有良好的绝缘性能,完全可代替云母和玻璃丝布,充当线圈和炉衬之间的绝缘保护层;胶泥材料的导热系数较高,不必担心相对较厚的胶泥层会影响热面炉衬的三层结。
第二,胶泥层位于线圈和保温层之间,正常情况下,环境温度很低(<300℃,偶尔有金属液接近其表面时胶泥层会释放出少量残余的水分,使绝缘电阻降低,系统提供早期报警。
第三,利用胶泥本身高于1800℃的耐火度,当偶尔有金属液渗漏到其表面时,胶泥能给线圈提供一层保护屏障,当出现报警时,胶泥层可提供一定的事故处理时间。
第四,对带有底顶出式的炉子而言,将胶泥制作成带有锥度的形状,避免了炉衬与线圈的摩擦,同时利用其强度对线圈进行固定,避免了线圈在使用和建、拆炉过程中的变形,延长了线圈的使用寿命。
第五,线圈与胶泥层作为炉子的耐火衬,虽一次性费用高,施工周期长,但其使用寿命可以与线圈相同,也可进行局部修补,因此就整体而言降低了筑炉成本。 干式打结炉衬前,首先在炉子线圈绝缘层内铺设一层石棉板和一层玻璃丝布,铺设时除手工平整压实各层材料外,还要用弹簧圈上下绷紧,捣固石英砂时,自上而下逐个移动弹簧圈,直至炉衬打结完毕。
打结炉底:炉底厚约280mm,分四次填砂,人工打结时防止各处密度不均,烘烤与烧结后的炉衬不致密。因此,必须严格控制加料厚度,一般填砂厚度不大于100mm/每次,炉壁控制在每次60mm以内,多人分班操作,每班4-6人,每次打结30分钟换人,围绕炉子缓慢旋转换位,用力均匀,以免造成密度不均。 炉底打结达到所需高度时刮平,即可放置坩埚模。对此,应注意保证坩埚模与感应圈同心,上下调整垂直,模样尽量与所筑炉底紧密结合,调整周边间隙相等后用三个木楔卡紧,中间吊重物压上,避免炉壁打结时石英砂产生位移。
打结炉壁:炉衬厚度为110-150mm,分批加入干式打结料,布料均匀,填料厚度不大于60 mm,打结15分钟(人工打结),直至与感应圈上缘平齐。在打结完后坩埚模不取出,烘干和烧结时起感应加热作用。
烘烤阶段:分别以200保温20分钟,300保温20分钟,400保温20分钟的速度将坩埚模加热至900℃,保温20分钟,目的是彻底排除炉衬中的水分。
半烧结阶段:分别以400保温20分钟,500保温20分钟,600保温20分钟必须控制升温速度,防止产生裂纹。
完全烧结阶段:高温烧结,坩埚的烧结结构是提高其使用寿命的基础。烧结温度不同,烧结层厚度不足,使用寿命明显降低。
2T中频炉在烘烤过程中加入了约950公斤铁料增强感应圈加热作用,随着烘烤与烧结的持续进行,通过低功率送电产生较为平稳的电磁力搅拌铁水,是炉衬上下受热均匀。严格控制石英砂三个相变区的温度,促进石英砂相变充分,提高了炉衬的首次烧结强度。烧结温度升高到1620℃后保温30分钟使其完全烧结。注意:第一次倾倒铁水是整炉的三分之一,第二次是整炉的一半。第三次才能全部倒完。千万不可第一次全部出炉!
三.小结 对于中频炉炉衬的寿命,除保证获得完整合理的三层炉衬外,还应注意平时的操作,筑炉是选用优质干净的筑炉材料,合理配比,精心打结,科学烘烤与烧结规范,严格操作工艺,即可延长炉子使用寿
上一篇:【[炉衬材料系列]】
下一篇:【高铝质捣打料(中性捣打料)】